
In-Space Manufacturing ISF Machine
For my Senior Project I am constructing a miniaturized incremental sheet (metal) forming machine, designed to operate in the vacuum of space.
Imagine a metal finger on an XYZ CNC gantry that pokes a piece of sheet metal into shape. That’s essentially what incremental sheet forming (ISF) is. My team and I built what we believe is the smallest ISF machine ever made.
ISF holds some promise as an in-space manufacturing process. This is because it has no fixed tooling (dies) and only locally deforms the workpiece, instead of all at once. This makes the machine much more compact and lightweight and allows for quicker and cheaper one-off parts, although production runs are much slower. As 3D printing is to injection molding, ISF is to sheet metal stamping. A space-based ISF machine could be used to produce all kinds of body panels or shielding for spacecraft (sheet stock is much easier to transport into space than an already-formed part).
My personal contributions included overall design of the motion system and the workpiece clamping system, as well as design and construction of the electronics/controls side of the machine. I also fabricated most of the waterjet parts (the plate-type parts) and a few of our machined parts (the extrusions and the passive X-axis guide blocks).
Some quick facts about our machine:
SPIF (single point incremental forming) machine with a fixed (non-rotating) tool
~35kg
~17”x22”x10” (designed to fit in a NASA EXPRESS locker for space transport)
Workpiece dimensions: 9x10”
Can fit up to 0.08” thick workpieces
Formable volume: 7x7x1”
Driven by 7 NEMA 23 stepper motors on 1.5mm pitch lead screws
Innovative automated quick-release workpiece fixturing system
Waterblock + heat pipe motor cooling system
Power consumption: <480W
Uses an entirely free and open-source software stack
UGS - Gcode sender/user interface
grbl - CNC firmware
CuraEngine - Toolpath generation
Python - Gcode editing/data collection
RPI OS - Operating system
Testing is still pending, but we have successfully formed thin (0.025”) sheets of aluminum and the motors barely broke a sweat, so we are confident that we can form greater thicknesses and tougher materials.
Currently, we are in the process of moving the machine into our vacuum chamber and adding some extra instrumentation to better understand the ISF process and the machine’s performance.
My team and I won 2nd place in the UNH ME Research judging category at the 2025 URC ISE. See my teammates’ LinkedIn profiles here:
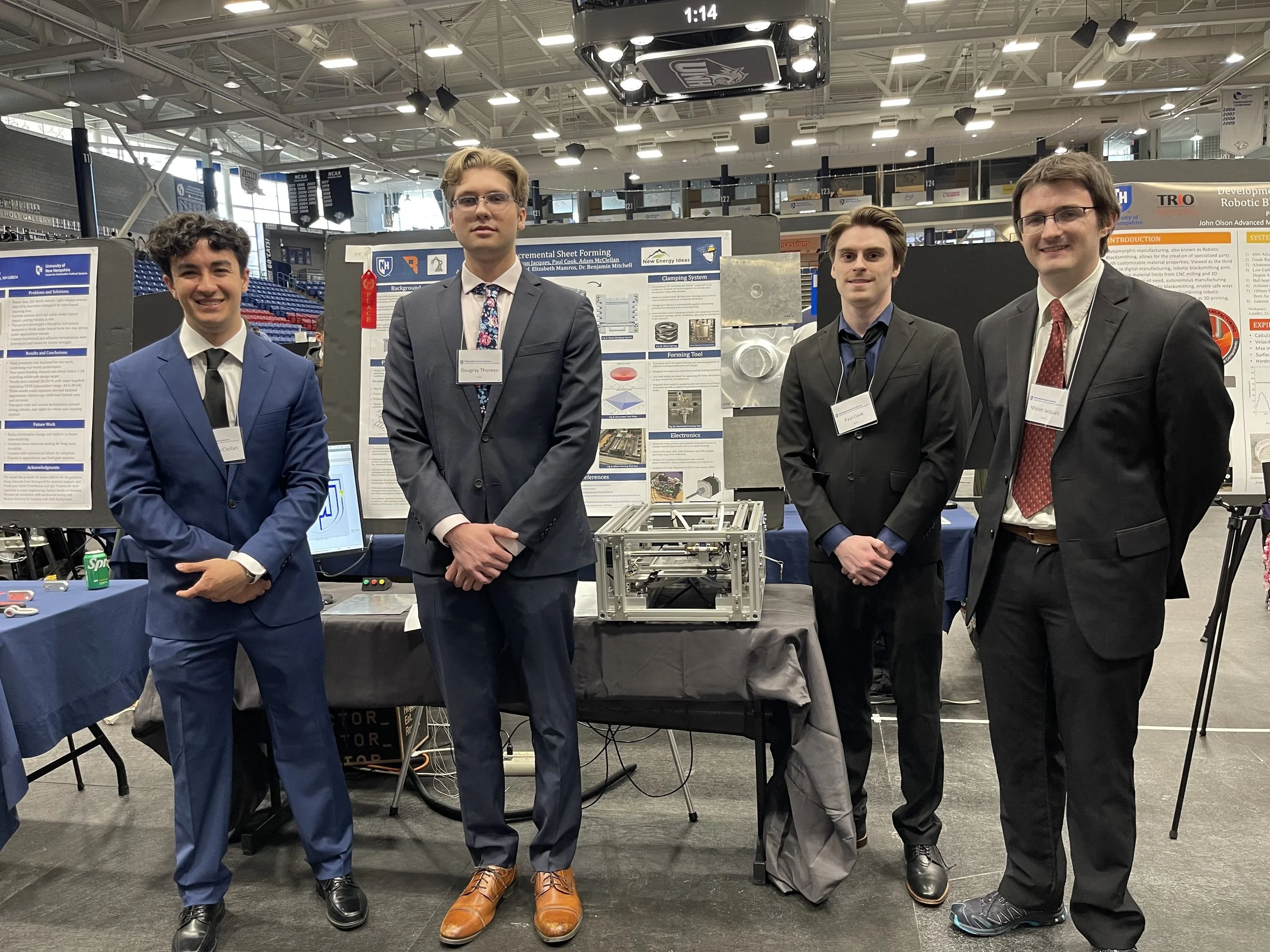
From left to right: Adam McClellan, Dougray Thoreen, Paul Cook, Mason Jacques

A couple of formed workpieces
An isometric view of the machine in SolidWorks

The machine as it was built.

Arduino #1 controls the core CNC functions (motor drivers, limit switches). Arduino #2 controls various ancillary functions (thermistors, relays to stop/start). The Raspberry Pi runs the Gcode sender and provides a nice CNC UI, as well as collects and displays the data gathered by Arduino #2. The entire setup is controlled by a single power switch for ease of use.